In this special guest feature, Jeremy Thomas from Lawrence Livermore National Lab writes that exascale computing will be a vital boost to the U.S. manufacturing industry.
Computer-aided design and engineering have come a long way since the first advanced CAD and CAE software programs appeared in the 1970s, and as manufacturing techniques, modeling and simulation have become increasingly complex over the years, computing power has had to keep up to meet the demand.
The need for exascale computing to handle the advanced physics and massive data sizes of today’s multimodal simulations is perhaps nowhere more apparent than in the product development industry. At Altair, a global software development and services company headquartered in Michigan with more than 2,600 employees and 68 offices worldwide, high-performance computing is essential to providing the company and its clients with the tools to optimize product design. Altair is a member organization of the DOE’s Exascale Computing Project (ECP) Industry Council, an external advisory group of prominent US companies helping to define the industrial computing requirements for a future exascale ecosystem.
Exascale will impact a wide range of US industries.
Through its proprietary CAE software suite HyperWorks and its HPC workload management solution PBS Works, Altair relies on HPC to explore the vast design space afforded by advanced manufacturing processes, and to study the physics behind the designs to validate them. Increasingly, Altair’s 5,000-plus customers — in industries ranging from automotive and aerospace to heavy equipment and high-end electronics — need simulations that combine multiple physics-based solvers to predict performance, including structural optimization, electromagnetics, and computational fluid dynamics.
One example is the auto industry, which is designing cars to adhere to stricter carbon emissions guidelines. Meeting these standards requires manufacturing lightweight vehicles that are also strong enough to meet crash ratings, meaning engineers need to simultaneously model processes such as fluid-structural interaction, thermal interaction and crash dynamics. Typically, these multidisciplinary simulations take a long time and use a lot of computational power. To truly optimize these combined studies, and get the results back quickly, Altair and other industry leaders will need a higher level of computation than is available today, according to the company’s Chief Technical Officer Sam Mahalingam.
The need for exascale really becomes extremely important because the size and complexity of the model increases as you do multiphysics simulations,” Mahalingam said. “This is a lot more complex model that allows you to truly understand what the interference and interactions are from one domain to another. In my opinion, exascale is truly going to contribute to capability computing in solving problems we have not solved before, and it’s going to make sure the products are a lot more optimized and introduced to the market a lot faster.”
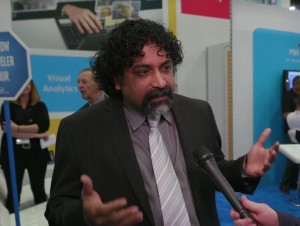
Sam Mahalingam, Altair
Multiphysics simulations also generate tremendous amounts of data. When launching a product, manufacturers typically go through several iterations of simulations, creating file sizes too large to download to desktop computers. While Altair has a large infrastructure of high performance machines to store data for validation and support its cloud-based storage, the sheer amount of data stretches the limits of existing hardware. Exascale machines might be able to store the data where it is generated and enable engineers to visualize it remotely, Mahalingam said.
The data you’re going to get cannot be visualized without exascale computing power and without parallelization,” he said.
While any product that is engineered or designed could benefit from exascale computing, Mahalingam said, it could be most transformational in industries where prototyping is difficult or impossible, such as aerospace or shipbuilding. Currently, companies in these industries must set up internal laboratories to test designs, which can be extremely cost-prohibitive. Exascale would allow for virtual labs that could completely simulate the physical experience, Mahalingam said, and instead of having to do individual studies sequentially, they could be done in parallel, saving time for engineers.
The benefits of exascale could even extend after a product launch, Mahalingam explained, when companies typically obtain real-world operational data and perform simulations to determine the remaining usable life of their products. If product developers could get the answer back in seconds instead of days, Mahalingam said, it could enhance preventative maintenance. “By superimposing the real-world operational data onto a digital model, we will be able to come back and predict where/when this part is going to fail depending on its design requirements.”
Today we model everything first and then we basically validate that model. But can we turn it around?” Mahalingam said. “Based on the real-world operational data we’re collecting, can we truly come out with a data-driven model, a prescribed model, as a starting point that we can say will deliver a design a lot faster?”
Mahalingam said exascale will be “critical” to running the deep learning and machine learning algorithms necessary to create data-driven models that are much closer to a final, polished model. Also, it will allow engineers to shrink the design space instantly because it will incorporate historical data. The result, Mahalingam said, is that engineers will be freed up to think about more complex problems to solve, and in turn come up with more innovative products.
To stay competitive, Mahalingam said, product development companies will need to scale up solvers and make sure multiphysics simulations work on next-generation systems. In preparation, Altair is already looking at newer programming paradigms like CHARM++, PMIx, as well as middleware designed for exascale applications. The company is exploring scheduling that will cater to exascale and is keeping close watch on hardware announcements.
Logistically, the move to exascale isn’t without its challenges in hardware, applications and software, Mahalingam said. Hardware will be challenged in meeting higher performance standards while using less power. As computing moves beyond Moore’s Law, software will need to be highly parallelized, and the onus will fall on resource managers to perform dynamic scheduling and place computing jobs as fast as they can to make full use of exascale capability. Systems will also need to be more “fault-tolerant,” Mahalingam said, and less dependent on a single node.
More broadly, exascale computing will likely shift the paradigm away from capacity computing (brute force/trial and error) to cognitive computing, Mahalingam said. From a national perspective, he added, exascale could have widespread implications, not just in manufacturing, but also life sciences, personalized medicine and agriculture.
It’s all about real time simulations, predicting what’s going to happen, and prescribing what needs to be done to make sure failures can be avoided or preempted,” Mahalingam said. “This is much bigger than any one company or any one industry. If you consider any industry, exascale is truly going to have a sizeable impact, and if a country like ours is going to be a leader in industrial design, engineering and manufacturing, we need exascale to keep the innovation edge.”